Эффективность применения аппаратов вихревого слоя АВС в процессах измельчения порошковых материалов
В ниже приведенном материале рассмотрено применение аппаратов вихревого слоя АВС для сухого измельчения и доизмельчения различных порошкообразных материалов: кварцевого песка, цемента, микромрамора, мела, доломита, диатомита. Экспериментально подтверждена высокая эффективность аппаратов вихревого слоя АВС (АВСП-100). Установлены некоторые технологические особенности помола в аппарате вихревого слоя порошкообразных материалов.
Огнеупоры, как формованные, так и неформованные, изготавливают из порошков различных минералов, размеры частиц которых должны быть в субмиллиметровом или даже нанодиапазонах ввиду влияния размера частиц на качество готового продукта. В настоящее время эти порошки получают преимущественно измельчением исходного сырья.
Измельчение производится такими наиболее распространенными способами, как изгиб, истирание, раздавливание, раскалывание, удар. В различных помольных устройствах разрушение твердых тел происходит одновременно несколькими способами, а именно комбинированным воздействием, но преобладающими являются один или два способа. Наиболее оптимальный способ измельчения выбирают, исходя из физических свойств твердого тела. На выбор способа измельчения также может оказывать влияние исходный размер частиц и в большей степени требуемый размер частиц, образующихся при помоле. Для производства огнеупоров помол исходного сырья производят в основном в шаровых мельницах. В них измельчение происходит преимущественно истиранием ― наименее эффективным способом диспергирования твердых тел [1].
В наши дни одним из наиболее эффективных по совокупности свойств оборудованием для измельчения являются аппараты вихревого слоя АВС-100, АВС-150 и АВСП-100, АВСП-150, изобретенные нашим инженером Д. Д. Логвиненко более 50 лет назад [2]. Удельная мощность, подводимая к единице объема, занимаемого вихревым слоем, достигает величины порядка 103 кВт/м3 [3]. Это на несколько порядков выше, чем, например, в рабочей зоне вибро- и шаровых мельниц. Наряду с этим у них нет узлов трения, их можно считать энергосберегающим оборудованием, так как удельный расход электроэнергии в них в 3‒5 раз меньше, чем, например, у шаровых мельниц.
Принцип работы аппарата вихревого слоя АВС: измельчение осуществляется ферромагнитными рабочими телами цилиндрической формы, помещенными в трубу из немагнитного материала, в которой создается вращающееся электромагнитное поле. Совокупность рабочих тел, вращающихся и соударяющихся в электромагнитном поле, образует так называемый вихревой слой, способный эффективно перемешивать и измельчать различные материалы. Несмотря на многие преимущества АВС перед другим мелющим оборудованием, они до сих пор не нашли широкого применения в промышленности.
Но значительное количество работ, опубликованных разными научными коллективами в последние годы, свидетельствует о росте интереса к установкам данного типа. Работы посвящены интенсификации процессов получения биодизельного топлива [2‒5], повышению прочности резины при механоактивации углеродных наполнителей [6], улучшению свойств цементов и бетонов [7‒10], получению ангидритовых вяжущих [11].
Улучшение свойств материалов, содержащих твердые частицы, в процессе обработки в аппарате вихревого слоя АВС связано, как правило, с измельчением этих частиц и активацией их поверхности. Например, в работе [6] после обработки в аппарате вихревого слоя АВС наблюдалось увеличение удельной поверхности различных углеродных наполнителей, входящих в состав резин, что способствовало повышению прочности резин на 40‒50 %. Также было доказано увеличение эффективности реакционно-способных упрочняющих добавок, которыми предварительно активировали углеродные наполнители в АВС.
В работе [8] было показано, что обработка в аппарате вихревого слоя АВС цементного теста приводит к росту прочности бетона и пенобетона на 36‒40 %, что объясняется увеличением доли мелкой (мельче 20 мкм) фракции частиц цемента с 44 до 71 %.
В работе [9] повышение прочности пенобетона за счет предварительной обработки рабочей суспензии из портландцемента в аппарате вихревого слоя АВС достигло 74 %, за счет сухого домола цемента его активность повысилась на 20 %. При получении ангидритового цемента в работе [11] обработка в АВС способствовала двукратному увеличению удельной поверхности, что увеличило прочность полученных мелкозернистых бетонов на 15‒20 % как в сухом, так и в водонасыщенном состоянии. Таким образом, во всех рассмотренных случаях положительный эффект от применения АВС частично или полностью связан с измельчением дисперсной фазы в вихревом слое. Однако основное внимание в большинстве работ, посвященных применению АВС, уделяется свойствам готовых материалов (резин, бетонов, затвердевших вяжущих). Цель работы ― исследование изменения гранулометрического состава в процессе сухого измельчения в АВС различных порошкообразных материалов. Результаты данного исследования могут быть использованы для объяснения причин улучшения свойств материалов, полученных с помощью АВС и для применения данных аппаратов для получения тонкодисперсных материалов.
ЭКСПЕРИМЕНТАЛЬНАЯ ЧАСТЬ
Материалы. Эксперименты по измельчению в АВС проводили на следующих материалах: кварцевый песок (Бурцевский карьер Нижегородской области), портландцемент ЦЕМ ΙΙ/А-Ш 32,5Н (ГОСТ 31108‒2003, ООО «Азия Цемент», Пензенская область, Никольский район, с. УстьИнза), микромрамор марок КМ-100 и КМ-60 (ТУ 5716-001-32524584, ООО «Батолит», Москва), диатомит (ТУ 5761-001-25310144, ООО «Диатомовый комбинат», г. Ульяновск), доломит (отсев через сито с размером ячейки 90 мкм от доломита ДМ-19-0,15 по ТУ 5743-001-75654417, ЗАО «Завод Ковровский доломит молотый», Владимирская обл., г. Ковров), мел ММС-2 (ГОСТ 101178, ОАО «Шебекинский меловой завод», Белгородская обл., г. Шебекино).
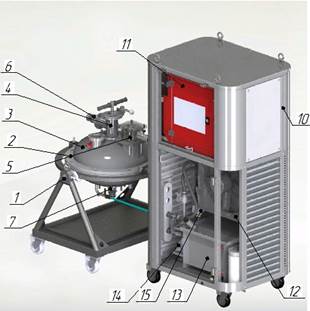
Обработка материалов в аппарате вихревого слоя АВС. Для измельчения использовался аппарат вихревого слоя АВС производства GlobeCore. Внешний вид аппарата показан на рис. 1. Все эксперименты проводили в периодическом режиме работы аппарат вихревого слоя АВС с помощью стакана из нержавеющей стали объемом около 500 мл. В стакан помещали навеску исследуемого порошкообразного материала и определенное количество ферромагнитных рабочих тел диаметром 2 мм и длиной 20 мм из закаленной стали, после чего стакан закрывали. Затем стакан предварительно встряхивали для равномерного распределения рабочих тел и обрабатываемого материала и помещали в рабочую камеру аппарата вихревого слоя АВС. Через определенные промежутки времени стакан вскрывали для отбора проб измельченного материала, после чего продолжали обработку.
Время обработки варьировали от 20 с до 3 мин. Методы исследований. Прямое определение размеров частиц и исследование их структуры проводили с помощью растрового электронного микроскопа «JEOL JSM-IT300LV». Гранулометрический состав исследуемых материалов определяли с помощью лазерного дифракционного анализатора размеров частиц «Shimadzu SALD-2300». Для проведения измерения небольшое количество исследуемого порошка диспергировали в воде в присутствии неионогенного ПАВ с помощью высокоскоростной мешалки и ультразвука. Полученная суспензия прокачивалась через измерительную ячейку прибора, где анализировалась по рассеиванию излучения красного лазера.
РЕЗУЛЬТАТЫ И ИХ ОБСУЖДЕНИЕ
На первом этапе исследований было проведено измельчение нескольких исследуемых материалов в стандартных условиях: насыпной объем исследуемого материала 145 см3 ; масса рабочих тел 254 г (около 520 шт.). На рис. 2 показаны дифференциальные функции распределения (F, %) частиц по размерам для карьерного песка с разной продолжительностью измельчения в аппарате вихревого слоя АВС.
В качестве основных показателей гранулометрического состава были выбраны медианный диаметр D50 (средний диаметр, по отношению к которому одна половина всех частиц пробы по массе будет крупнее, а другая ― мельче) и диаметр D98 (диаметр, по отношению к которому 98 % всех частиц пробы по массе будут мельче).
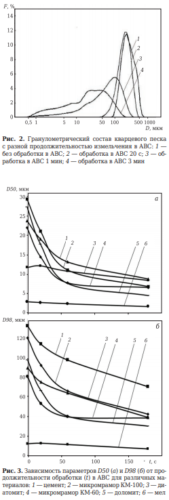
с разной продолжительностью измельчения в АВС
Данные по гранулометрическому составу проб песка в целом позволяют убедиться, что в ходе обработки в АВС достаточно быстро происходит уменьшение как среднего, так и максимального размеров частиц. Кварцевый песок является трудно измельчаемым материалом по причине высокой твердости (6‒7 единиц по шкале Мооса). Поскольку в традиционно применяемом оборудовании ― шаровых мельницах используют способ истирания, то для песка это наименее эффективный способ измельчения. Благодаря тому, что в АВС для измельчения используется ударное воздействие, за 3 мин размер частиц D50 уменьшается с 235 до 22 мкм, а D98 ― с 498 до 133 мкм. В шаровых мельницах на это затрачивается несколько часов.
На рис. 3 показаны зависимости показателей D50 и D98 от времени обработки в АВС других исследуемых материалов с меньшим исходным размером частиц. Зависимости демонстрируют эффективность измельчения в АВС различных материалов с разной твердостью. Измельчение происходит особенно быстро до среднего размера частиц 8‒12 мкм, после чего замедляется, причем дальнейшая скорость измельчения близка для разных материалов, о чем свидетельствует схожий наклон кривых.
Для подтверждения результатов, полученных на дифракционном лазерном анализаторе, и изучения структуры частиц, полученных в результате измельчения, были проанализированы микрофотографии исходных материалов и продуктов их помола в АВС в течение 3 мин (рис. 4). Особенно показательными являются микрофотографии для кварцевого песка (см. рис. 4, а). Они полностью подтверждают результаты, полученные на дифракционном лазерном анализаторе, и свидетельствуют об уменьшении среднего размера частиц более чем в 10 раз. Микрофотографии образцов доломита, измельченного в АВС (см. рис. 4, б), подтверждают отсутствие крупных частиц, имеющихся в исходном доломите, что также согласуется с результатами, полученными на лазерном анализаторе.
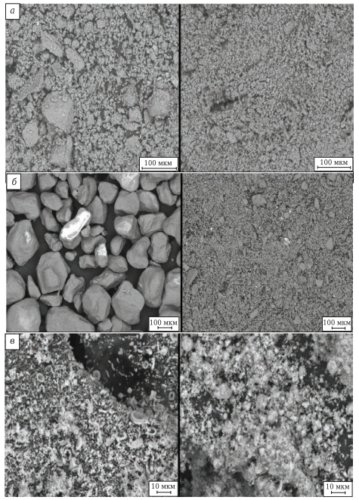
Для мела изменение размеров частиц не столь значительно, поэтому и на микрофотографиях трудно зафиксировать различия этого параметра. Однако на микрофотографиях обработанного в АВС мела (см. рис. 4, в) по сравнению с исходным образцом полностью отсутствуют характерные для него структуры в виде колец (обусловленные зоогенным происхождением мела), что свидетельствует об их разрушении в процессе измельчения.
Микрофотографии для других исследованных материалов подтверждают результаты, полученные с помощью дифракционного лазерного анализатора размеров частиц. Таким образом, показана высокая эффективность измельчения в АВС различных, в том числе трудно измельчаемых, материалов в разных диапазонах размеров частиц. На примере микромрамора марки КМ-100 изучено влияние ряда технологических параметров на эффективность измельчения: соотношение массы рабочих тел и массы обрабатываемого материала, степень заполнения рабочей камеры (колбы) АВС. Ниже представлены зависимости гранулометрических показателей D50 и D98 от продолжительности измельчения: ‒ при различной массе рабочих тел и постоянной массе навески микромрамора (рис. 5); ‒ при постоянной массе рабочих тел и разных массах навески микромрамора (рис. 6);
‒ при постоянном соотношении массы рабочих тел и массы навески микромрамора, но разной общей массе смеси (рис. 7). Анализ полученных данных позволяет выявить некоторые закономерности для подбора оптимальных условий измельчения. Увеличению эффективности измельчения способствует как увеличение количества рабочих тел по отношению к микромрамору (см. рис. 5), так и общее увеличение загрузки колбы АВС (см. рис. 7). Одновременно с этим изменение массы микрокальцита при постоянном количестве рабочих тел в колбе аппарата вихревого слоя АВС (см. рис. 6) мало влияет на эффективность измельчения. Таким образом, можно сделать вывод, что эффективность измельчения порошкообразных материалов в АВС повышается с ростом количества рабочих тел, находящихся в рабочей камере, и мало зависит от количества обрабатываемого материала. Однако повышение количества рабочих тел и обрабатываемого материала допустимо лишь до определенного критического значения заполнения колбы, после которого рабочие тела начинают мешать движению друг друга или избыток обрабатываемого материала занимает практически все свободное пространство, препятствуя разгону рабочих тел в начальной стадии движения. В данном эксперименте критическим является количество рабочих тел 800‒1000 шт. (390‒490 г) в зависимости от навески микрокальцита или 300‒400 г микрокальцита в зависимости от количества рабочих тел.
ЗАКЛЮЧЕНИЕ
Проведенная работа показала высокую эффективность использования аппарата вихревого слоя АВС в процессах сухого помола и домола различных порошков как для целей получения тонкодисперсных материалов в качестве самостоятельных товарных продуктов, так и в составе других материалов. Установлено, что скорость помола в аппарате вихревого слоя АВС существенно зависит от степени заполнения рабочей камеры аппарата вихревого слоя АВС ферромагнитными телами и мало зависит от количества обрабатываемого материала.
Данная подборка выполнена при поддержке ФЦП “Исследования и разработки по приоритетным направлениям развития научно-технологического комплекса России на 2014‒2020 годы», проект № RFMEFI57815X0135.
Библиографический список
- Логвиненко, Д. Д. Интенсификация технологических процессов в аппаратах с вихревым слоем / Д. Д. Логвиненко, О. П. Шеляков. ― Киев : Техника, 1976. ― 144 с.
- Нагорнов, С. А. Исследование процесса получения биодизельного топлива в проточном аппарате с магнито–вихревым слоем ферромагнитных частиц / С. А. Нагорнов, С. И. Дворецкий, С. В. Романцова [и др.] // Вестник ТГТУ. ― 2013. ― Т. 19, № 2. ― С. 316.
- Нагорнов, С. А. Моделирование гидродинамики в реакторе с вихревым слоем ферромагнитных частиц при синтезе биотоплива / С. А. Нагорнов, Д. С. Дворецкий, С. И. Дворецкий, А. А. Ермаков // Вопросы современной науки и практики. Университет им. В. И. Вернадского. ― 2010. ― № 10/12 (31). ― С. 359.
- Нагорнов, С. А. Моделирование процесса метанолиза растительных масел в аппарате вихревого слоя ферромагнитных частиц / С. А. Нагорнов, Д. С. Дворецкий, С. И. Дворецкий, А. А. Ермаков // Вестник ТГТУ. ― 2010. ― Т. 16, № 4. ― С. 944.
- Мамедова, Т. А. Особенности получения биодизеля первого поколения в аппарате с вихревым слоем / Т. А. Мамедова, А. Г. Талыбов, Н. К. Андрюшенко [и др.] // Вестник МИТХТ им. М. В. Ломоносова. ― 2011. ― Т. 6, № 6. ― С. 65.
- Ершов, Д. В. Механохимическая активация углеродных материалов в аппарате с вихревым слоем / Д. В. Ершов // Химия и химическая технология. ― 2008. ― Т. 51. Вып. 11. ― С. 81.
- Явруян, Х. С. Гомогенизация наномодифицированных цементных систем и подбор параметров их обработки в установках с вихревым слоем / Х. С. Явруян, И. А. Филонов // Вестник МГСУ. ― 2013. ― № 2. ― С. 130.
- Торлина, Е. А. Электромагнитная активация цементного теста и пенобетонной смеси / Е. А. Торлина, А. И. Шуйский, Г. А. Ткаченко [и др.] // Вестник МГСУ. ― 2012. ― № 12. ― С. 149.
- Филонов, И. А. Механическая активация портландцемента в аппарате вихревого слоя / И. А. Филонов, Х. С. Явруян // Инженерный вестник Дона. ― 2012. ― № 3 (21). ― С. 678.
- Шаяхмедов, Р. И. Серобетон и аппарат вихревого слоя / Р. И. Шаяхмедов, А. П. Журавлев // Перспективы развития строительного комплекса. ― 2012. ― Т. 1. ― С. 19.
- Мирская, М. В. Аппараты вихревого слоя в производстве безобжиговых ангидритовых вяжущих / М. В. Мирская // Инженерный вестник Дона. ― 2008. ― Т. 4, № 2. ― С. 66.